In my research into advancing hydrogen as a green energy carrier, I found a new scientific research report (A review of gas phase inhibition of gaseous hydrogen embrittlement in pipeline steels) that delves into a critical challenge that dramatically affects the sector: hydrogen embrittlement (HE) in steel pipelines.
HE poses a significant risk to the integrity of pipelines used for hydrogen transport, leading to premature failure. The report presents a nuanced analysis of gas phase inhibition as a strategy to mitigate this issue, focusing on the addition of small amounts of gases such as oxygen (O2), carbon monoxide (CO), and sulfur dioxide (SO2) to the hydrogen stream. It is one solution of many that have been suggested over the years.
Gas inhibitors reduce the risk of HE, thereby enhancing the safety and longevity of steel pipelines for hydrogen transport. This finding is particularly relevant as the world moves towards cleaner energy sources, and hydrogen infrastructure is expected to expand.
However, the report also highlights a significant challenge in the field: the inconsistency of research outcomes, mainly attributed to the diverse mechanical testing methods employed across studies. This inconsistency underscores the necessity for a more standardised approach to evaluating the effectiveness of gas-phase inhibition.
To address this, the report advocates for adopting gas phase permeation studies. Such studies offer a quantifiable measure of inhibition effectiveness, providing a more reliable and standardised method for assessing the viability of gas phase inhibitors in preventing HE. This approach could be crucial in safely adapting existing natural gas pipelines for hydrogen transport, a critical step in transitioning to a hydrogen-based energy system.
The report sheds light on a promising method to mitigate a longstanding issue by bridging the gap between research inconsistencies and practical applications. It paves the way for a more systematic and reliable exploration of gas phase inhibition. This advancement is essential for ensuring the safe, efficient, and sustainable transport of hydrogen, marking a noteworthy stride towards realising hydrogen as a cornerstone of the future energy landscape.
The report also highlights that the industry continues to need help solving the issue of hydrogen embrittlement (HE) in the quest for sustainable hydrogen energy. HE in steel pipelines continues to be a significant hurdle, threatening the integrity and safety of hydrogen transport infrastructure.
But there is another solution…
The innovative minds at Triton Hydrogen have introduced Tritonex, a groundbreaking solution that addresses this challenge head-on. As the world’s first ISO 17081:2014 certified Hydrogen Barrier Coating, Tritonex boasts zero percent hydrogen permeation, marking a revolutionary advancement in the sector.
Tritonex’s nano-technology coating is hailed for its ability to shield against HE, diffusion, degradation, and corrosion, thereby enhancing the longevity and safety of hydrogen pipelines. This innovative protection aligns with the global push towards sustainable energy utilisation. It significantly reduces total ownership costs across the hydrogen value chain, making hydrogen operations more economically viable.
Moreover, Tritonex offers unprecedented design freedom, opening up new possibilities in material and design choices that can reduce carbon footprints and improve operational efficiency.
The introduction of Tritonex by Triton Hydrogen is creating a buzz among experts worldwide, offering a versatile, non-toxic, and environmentally friendly solution with unmatched anti-corrosion properties. It’s a testament to the company’s commitment to enhancing efficiency and embracing sustainability in the hydrogen industry, setting a new standard for safety and sustainability in hydrogen transport.
Read the full report:
A review of gas phase inhibition of gaseous hydrogen embrittlement in pipeline steels
International Journal of Hydrogen Energy, 26 February 2024
Maximilian Röthig a,∗, Joshua Hoschke a, Clotario Tapia a,b, Jeffrey Venezuela a, Andrej Atrens a,∗
a School of Mechanical and Mining Engineering, Centre for Advanced Materials Processing and Manufacturing (AMPAM), The University of Queensland, St Lucia, Brisbane, Australia
b Faculty of Mechanical Engineering and Production Science, Escuela Superior Politécnica del Litoral (ESPOL), Guayaquil, Ecuador
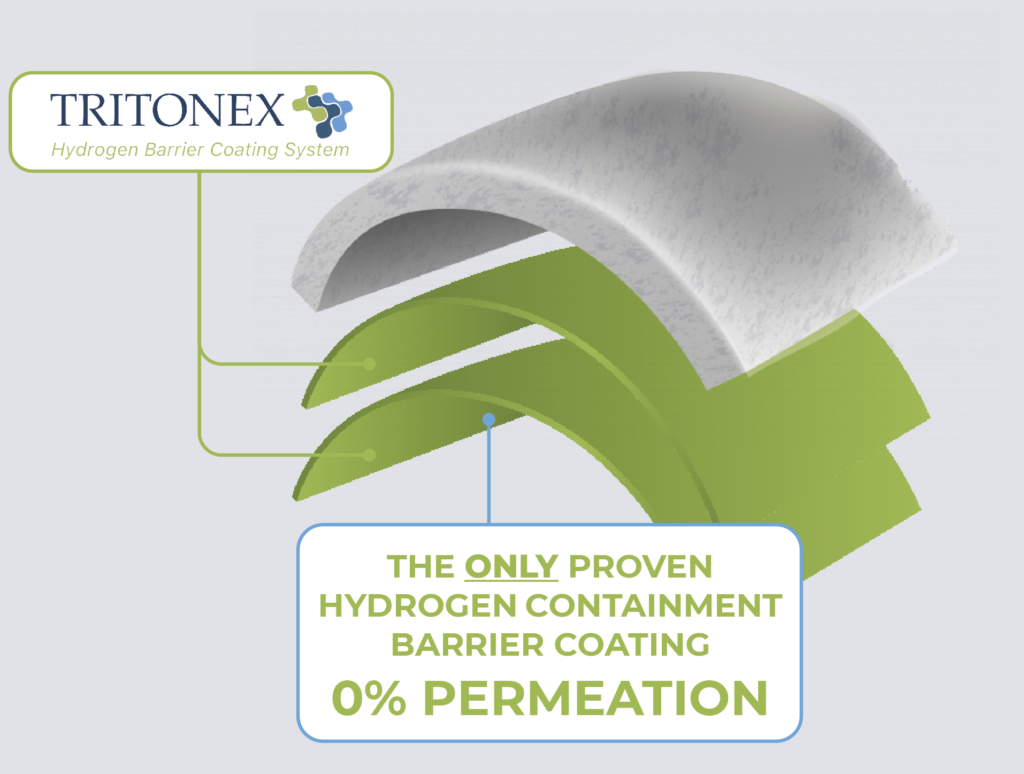